Power of Prototyping: EDC Friction Folder Update
- gondekedc
- Apr 7, 2021
- 2 min read
For those who don’t know my day job is an engineer in manufacturing. I have been in the industry for about 10 years at the time of writing this and learned a lot during my time. One of the main lessons I learned was from a project at my last job that involved a large automotive battery tray. This tray utilized new technologies and processes our company was still learning. We made prototypes for our customer in a way that was differently planned than how we wanted to make the production parts. This led to huge problems during our initial production runs which caused me a lot of headaches.
I carried that lesson from my day job to GondekEDC. We always prototype all our products (metal and non-metal) to make sure they can be produced to our high standards in an efficient manner. There have been times where this was very productive such as with the Reaper. The initial design did not work well in pulling out nails and the design needed to be modified for the product to function as intended.
When it came to our EDC friction folder prototyping wasn’t even a question and we kicked off two metal prototypes about a month ago. These were to be built exactly like the production ones using titanium for the scales and sv35 for the blade. When we received these prototypes, they looked amazing but there were some initial fitting issues with the pivot and the newly added backspacer. The pivot holes in the scales were about 0.001”- 0.002” too small (about ½ the width of a human hair). This is a simple machining change but good to catch now to make the required changes. The backspacer fits but it’s a little too snug and we prefer it to be easier for assembly. A little more clearance will be added to that component as well. The lesson learned on this one is to send a few assembly components to the machine shop to try the fit in order to catch this even sooner.
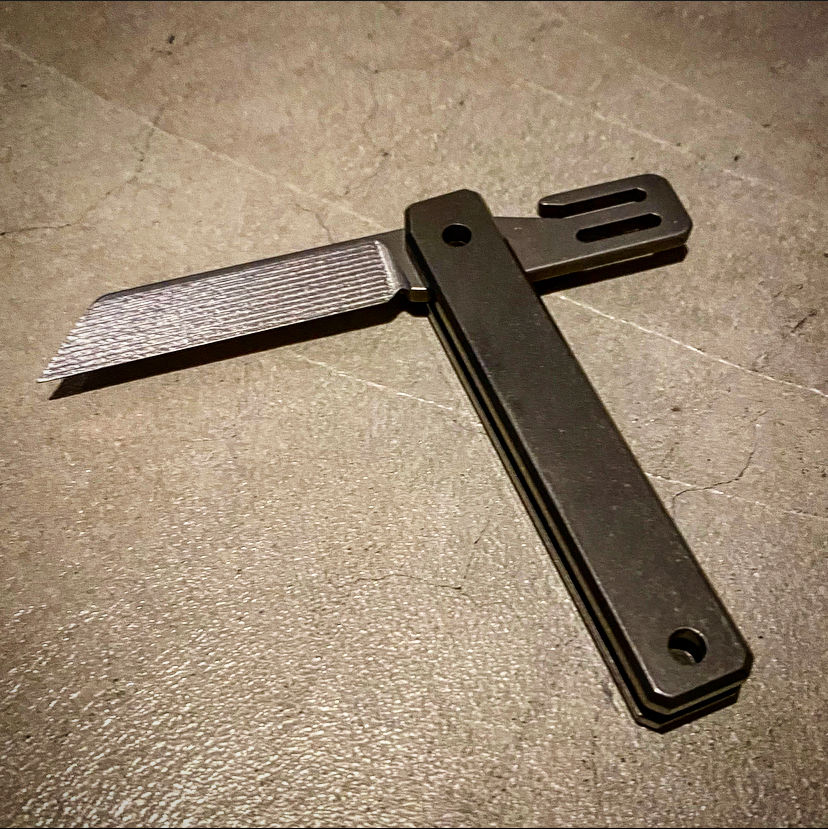
These are very small changes but finding them out earlier than later will save time and money in this project. That allows a smoother release when the time comes and the ability to make it as affordable as possible. The next steps are to purchase a reamer to open the holes slightly, finish the blade, and send it to heat treat. If all goes well, we plan on selling one of them as an early release! Still about a month or so from that point but we are continuing to make progress.
That's a great shape! Maybe offer with a bead + folder package deal :) Price is regular, but you connect the two